Diagnostyka wyrobów i urządzeń wykonanych z metali ferromagnetycznych
prowadzona metodą Magnetycznej Pamięci Metalu (metodą MPM)
W Rosji w latach 1985-1990 opracowano całkiem nową metodę diagnostyki wyrobów i przemysłowych urządzeń technicznych, opartą na efekcie magnetycznej pamięci metalu. W Polsce na przełomie lat 1989-90 rozpoczęto pierwsze prace badawcze metodą Magnetycznej Pamięci Metalu (metodą MPM).
Określono warunki formowania pozostałości magnetycznej metalu, odzwierciedlającej strukturalną pamięć magnetyczną oraz stan naprężeń i odkształceń wyrobów metalowych. W metodzie MPM wykorzystane są zależności magnetyczno-energetyczne tzw. własnego pola magnetycznego metalu utworzonego w trakcie zachodzących przemian w budowie i wielkości oraz rozkładzie domen magnetycznych podczas oddziaływania sił zewnętrznych.
Poniżej opisano pierwsze początkowe kryteria wykorzystywane w diagnostyce wyrobów za pomocą metody magnetycznej pamięci metalu. Określają one strefy koncentracji naprężeń (KN) na powierzchni badanego wyrobu charakteryzujące się zmianą znaku pola namagnesowania Hp wzdłuż linii pola, na której to składowa normalna (prostopadła) pola Hpy przyjmuje wartość zerową Hpy=0 [A/m].
Na stronie podajemy przykłady praktycznego zastosowania kryterium dla wczesnej diagnostyki uszkodzeń zmęczeniowych wyrobów lub przemysłowych urządzeń technicznych. Skrótowo przedstawione są: historia i teoria badania nieniszczącego ferromagnetyków metodą magnetycznej pamięci metalu (MPM).
Zdjęcie ilustruje diagnozowanie urządzeń metodą MPM - widać, że
badanie metodą MPM nie wymaga żadnego przygotowania powierzchni diagnozowanego rurociągu
Wiadomo, że koncentracja naprężeń (KN) powstająca w efekcie różnorodnych obciążeń powoduje uszkodzenia, wśród których najbardziej intensywne są procesy korozji, zmęczenia i pełzania.
Odlewanie, kucie i obróbka termiczna metalu odbywają się w temperaturze powyżej punktu Curie (768°C), po przekroczeniu którego całkowicie zanika pozostałość magnetyczna. Podczas późniejszego ochładzania metalu poniżej punktu Curie (ochładzanie odbywa się zazwyczaj w polu magnetycznym Ziemi) wraz z krystalizacją metalu na skutek efektu magneto-mechanicznego formuje się magnetyczna tekstura wyrobu. Pojawienie się w niej tak zwanych Stref Koncentracji Naprężeń czyli obszarów koncentracji naprężeń wewnętrznych w wyrobach ferromagnetycznych może być spowodowane samą technologią ich wykonania.
W ten sposób powstaje strukturalna pamięć metali czyli pozostałość magnetyczna związana z budową struktury krystalicznej, wymiarem ziarna oraz z niejednorodnościami wywołanymi występowaniem domieszek innych metali. Nazwano ją Magnetyczną Pamięcią Metalu, i opracowano metodę praktycznego wykorzystania wiedzy o tym zjawisku.
W podstawowym zakresie wyjaśniają to przedstawione niżej grafiki i ich opisy.
Linie Koncentracji Naprężeń KN i ich znaczenie dla diagnostyki urządzeń technicznych (Rys. 1,2,3)
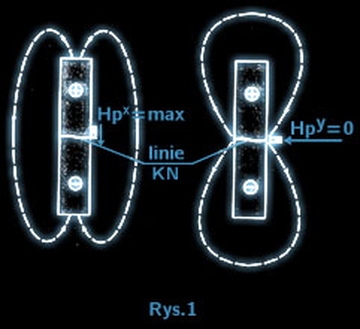
W miejscach największej koncentracji wad i niejednorodności w metalu wyrobu (w zewnętrznym polu Ziemi) pojawiają się węzły zamocowania domen, które wykształcają sumaryczne, magnetyczne pole rozproszone odczytywane na powierzchni wyrobu. Poślizg dyslokacji, dzięki któremu odbywa się formowanie struktury metalu i ostatecznego namagnesowania, określa w rezultacie koncentrację wewnętrznych naprężeń. W miejscu koncentracji wad (i związanych z nimi koncentracji naprężeń wewnętrznych) magnetyczne przenikanie metalu staje się minimalne, a na powierzchni wyrobu wykształca się maksymalne magnetyczne pole rozproszone. Składowa styczna tego pola Hpx w strefie KN ma wartość maksymalną, a składowa normalna Hpy przechodząc przez wartość zerową zmienia znak. Podczas skanowania wzdłuż powierzchni wyrobu czujnikiem przyrządu (miernikiem) możliwe staje się określenie linii koncentracji naprężeń (linii KN) (Rys. 1).
Poziom koncentracji naprężeń wewnętrznych określa wielkość pola Hp, która jest zgodna z kierunkiem zachodzących zmian domen zamykających na powierzchni wyrobu. Wiadomo, że domeny zamykające skierowane są wzdłuż trudnej osi namagnesowania, i dlatego wielkość Hp charakteryzuje energię anizotropii spowodowaną niejednorodnością struktury.
Wzdłuż linii KN na konkretnych wyrobach, w zależności od swojego położenia względem kierunku działania zewnętrznego obciążenia i do zewnętrznego pola magnetycznego (pola Ziemi), zachodzą zmiany właściwości mmetalu. Próbka z prostopadłym położeniem linii KN względem kierunku zewnętrznego obciążenia ma obniżoną wytrzymałość w porównaniu z próbkami, na których linia KN położona jest pod kątem lub współosiowo z obciążeniem. Dla potwierdzenia tego założenia przeprowadzone były specjalne badania na próbkach ze stali ferromagnetycznej na zrywarce wytrzymałościowej.
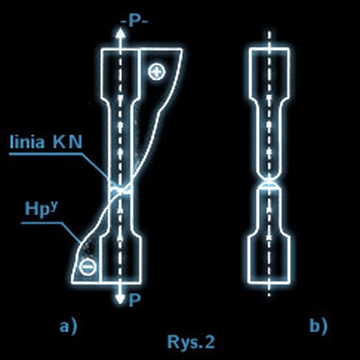
Rys. 2a) przedstawia rozkład Hpy wzdłuż osi próbki na jej powierzchni przed wstawieniem w zaciski zrywarki i rozkład linii Hpy=0, charakteryzującej linię KN przed rozpoczęciem badań. Próbkę badano na rozciąganie przykładając siłę P prostopadle do linii KN.
Na rys. 2b) widać, że rozerwanie próbki nastąpiło praktycznie po linii KN (Hpy=0).
Analogiczne wyniki badań otrzymano na różnych próbkach ze stali ferromagnetycznych.
Wiadomo, że szyjka pojawia się w "najsłabszym" miejscu próbki. W miejscu formowania się szyjki na próbce (przecięcie Hpy=0) następuje szybkie przemieszczenie się dyslokacji, które powoduje pojawienie się mikropęknięć - zaczątków zniszczenia. Mechanizm kształtowania szyjki na próbce i następnie jej rozerwania jest dobrze opisany w literaturze. Jednak wyjaśnienia, dlaczego szyjka pojawia się właśnie w tym miejscu konkretnej próbki, w literaturze niestety nie było, aż do początku lat 90. ubiegłego stulecia.
Przeprowadzone eksperymenty pozwalają odpowiedzieć na to pytanie. W próbkach z wyraźną linią KN, położoną prostopadle do kierunku zewnętrznego obciążenia, pojawienie się szyjki i rozerwanie próbki następuje dokładnie po linii KN. W tych przypadkach, gdy linia KN na próbkach była położona wzdłuż jej osi lub koncentracja naprężeń (intensywność zmiany wielkości Hpy) była nieznaczna, miejsca pojawiania się szyjki, a następnie rozerwania próbek najczęściej nie były zgodne z liniami KN. Jednocześnie w różnych doświadczeniach, w miarę zwiększania obciążeń obserwowano przemieszczenie linii Hpy=0 w miejsce pojawiania się szyjki na próbce.
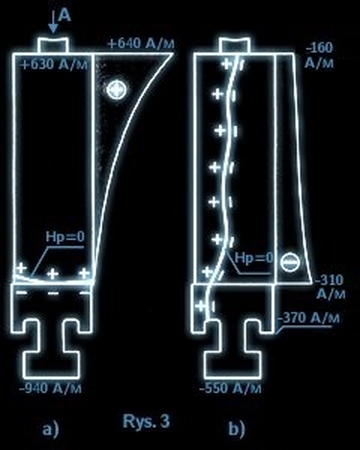
Rys. 3a) przedstawia linię KN (Hp=0) położoną u podstawy łopatki turbiny parowej i przebiegającą prostopadle do odśrodkowej siły roboczej. Takiej łopatki nie należy dopuścić do eksploatacji. Z kolei Rys. 3b) przedstawia inną linię KN (Hp=0) przebiegającą wzdłuż korpusu łopatki i nie stanowiącą zagrożenia.
Opisany wcześniej parametr, charakteryzujący się zerową wartością normalnej składowej magnetycznego pola rozproszonego, jest przydatny do określenia Stref Koncentracji Naprężeń SKN w urządzeniach będących w stanie eksploatacji, np.: rurociągi, dowolne zbiorniki lub konstrukcje metalowe. Występująca na pracujących częściach maszyn i urządzeń pamięć magnetyczna metalu jest wynikiem przykładanych obciążeń i zaistniałych zmian strukturalnych. Obciążenia wywołują znaczące zmiany wielkości i kierunku namagnesowania metalu.
Na podstawie wielu takich badań (Rysunki 1, 2, 3 i dalsze) w drugiej połowie lat 80⋅tych w Rosji, w zespole prof. Anatolija A. Dubova opracowana została szybka i efektywna metoda diagnostyki części maszyn i wyrobów według ich podatności na uszkodzenia w czasie eksploatacji.
Spostrzeżenia i badania które pozwoliły wynaleźć nową metodę diagnostyki urządzeń technicznych wykonanych z ferromagnetyków
W miejscu zniszczenia rury kotłowej (system energetyczny Wołgogradu) zaobserwowano silne namagnesowanie.
Rys. 4a przedstawia kawałek metalu z miejsca zniszczenia, który przyciąga opiłki tak jak silny magnes. Wtedy postawiono pytanie: skąd wzięło się to silne namagnesowanie w miejscu zniszczenia rury? Analogiczny efekt przedstawia Rys. 4b.
Badania laboratoryjne i przemysłowe wykazały, że poziom i rozkład pozostałości magnetycznej (i odpowiadającego jej magnetycznego pola rozproszonego na powierzchni kontrolowanych urządzeń) uwarunkowane są występowaniem efektu magneto-sprężystego lub efektu magneto-mechanicznego.
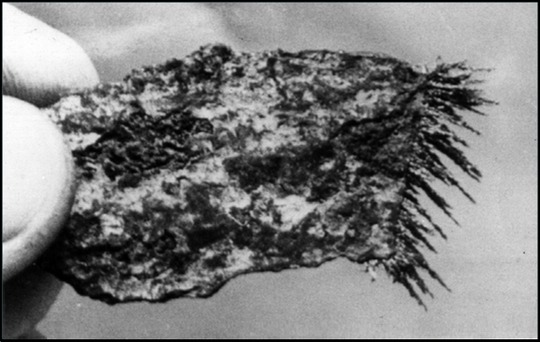
Rys. 4a. Kawałek zniszczonej rury kotłowej działa jak magnes
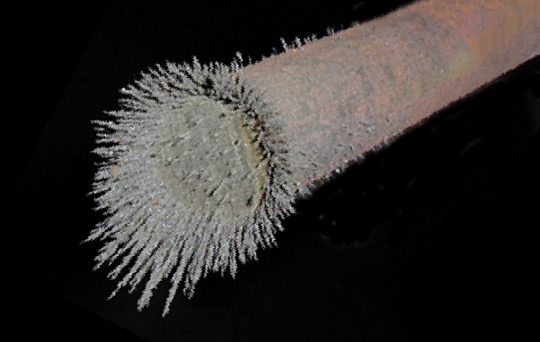
Rys. 4b. Urwany pręt stalowy także przyciąga metalowe opiłki
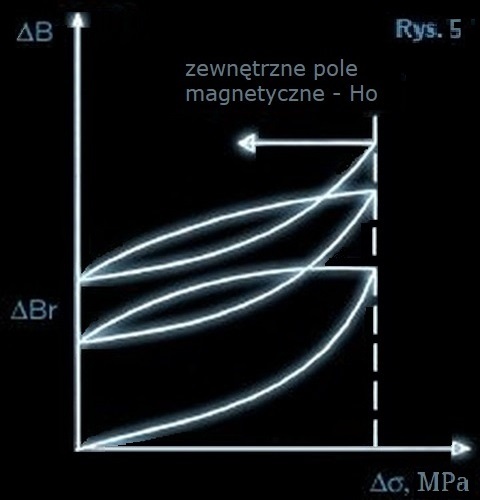
Rys. 5 przedstawia Schemat efektu magnetycznego:
ΔBr - cykliczny przyrost indukcji magnetycznej, aż do osiągnięcia stanu nasycenia;
Δσ - zmiana cyklicznej siły obciążającej urządzenie, wyrób, konstrukcję;
Ho - zewnętrzne pole magnetyczne, którym jest pole magnetyczne Ziemi.
Na Rys. 5. pokazano schemat ujawniania się efektu magnetycznego. Jeśli na urządzenie działa cykliczna siła Δσ (co zachodzi w zewnętrznym, ziemskim polu magnetycznym), to w urządzeniu następuje wzrost ostatecznego namagnesowania - indukcji ΔB.
W efekcie oddziaływania cyklicznych lub wibracyjnych obciążeń w urządzeniach następuje znaczny wzrost namagnesowania metalu. Zawsze jest to zjawisko niepożądane, gdyż grozi uszkodzeniem lub zniszczeniem urządzeń.
Przypomninamy, że firma RESURS, termin - urządzenie przemysłowe, a ściślej obiekt przemysłowy wykonany z metali ferromagnetycznych interpretuje jako:
maszyny i ich elementy, urządzenia mechaniczne, urządzenia energetyczne i ciepłownicze, konstrukcje stalowe, zbiorniki ciśnieniowe - w tym wszelkie połączenia spawane.
Po ujawnieniu silnego namagnesowania rur kotłowych w Wołgogradzie po raz pierwszy zaproponowano zastosowanie tego zjawiska do celów diagnostycznych. Na Rys. 6 pokazano rozłożenie pola ostatecznego namagnesowania wzdłuż rur kotłowych. Powstałe pole magnetyczne odzwierciedla naprężenia i odkształcenia rur pojawiające się podczas pracy kotłów energetycznych.
Rys. 6 przedstawia wybrane rezultaty badania trzech rur kotła energetycznego, z których każda inaczej reagowała na obciążenia wywołane wysoką temperaturą, ciśnieniem pary, brakiem samokompensacji w miejscach podparcia (zamocowania), itd. Te wyniki badań pokazują jak kompleksowa jest to metoda badań nieniszczących - metoda MPM przy diagnozowaniu obiektów przemysłowych typu urządzenia ciepłownicze.
Wyjaśniamy symbole zastosowane na rysunku:
Rura nr 41:
1 - miejsca zamocowania rury;
2 - specjalistyczny przyrząd pomiarowy - diagnozowano nim każdą rurę kotła na odcinku kontrolnym o długości 5300 mm;
A, D, E - miejsca zmiany znaku magnetycznego pola rozproszonego - miejsce zachodzących odkształceń (deformacji);
B, F - miejsca z maksimum natężenia (A/m) magnetycznego pola rozproszonego wskazujące na eksploatacyjne wytężenie metalu rur.
Wniosek: rura z grupy rur najbardziej narażonych na uszkodzenie. Należy ją nadal monitorować ze zwiększoną częstotliwością lub zastosować kolejne badania NDT w celu określenia aktualnego stanu technicznego rury.
Rura nr 17:
1 - miejsca zamocowania rury.
Wniosek wynikający z wykresu: zamocowania rury działały prawidłowo, groźnych koncentracji naprężeń nie wykryto.
Rura nr 31:
1 - miejsca zamocowania rury;
Sp - spoina montażowa;
3 - ujawnione miejsce korozji zewnętrznej metalu rury.
Wniosek: rura z grupy rur średnio narażonych na uszkodzenie - należy ją nadal monitorować ze zwiększoną częstotliwością lub zastosować kolejne badania NDT w celu określenia aktualnego stanu technicznego rury.
Zastosowanie badań metodą Magnetycznej Pamięci Metalu (metodą MPM)
Podczas badań ustalono również, że zmiana pozostałości magnetycznej i zmierzonego magnetycznego pola rozproszonego podczas rozciągania, ściskania, skręcania lub cyklicznych obciążeń wyrobów ferromagnetycznych jest jednoznacznie związana z maksymalnymi działającymi naprężeniami i odkształceniami - a to pozwala wykorzystać ten parametr do opracowania konkretnej metody diagnostyki.
Zazwyczaj w realnych warunkach pracy rur pod działaniem obciążeń pojawia się zmniejszenie wytrzymałości metali. W najbardziej osłabionych przekrojach rury wykształcają się koncentracje naprężeń i odkształceń. W tych przekrojach pojawiają się skupiska poślizgu dyslokacji - i to na długo przed osiągnięciem granicy plastyczności metalu.
Badanie za pomocą zaproponowanej metody diagnostyki można wykonywać podczas pracy urządzeń i co jest ważne - nie jest wymagane jakiekolwiek przygotowanie kontrolowanych powierzchni.
Badanie metodą Magnetycznej Pamięci Metalu (metodą MPM) zalicza się do metod szybkich. Specjalistyczne, miniaturowe przyrządy z ekranem i czujnikiem pozwalają wykonać badanie rurociągu z szybkością 100m/1h i więcej.
Podstawowym zadaniem badania metodą MPM jest zdefiniowanie na obiekcie najbardziej niebezpiecznych odcinków i węzłów charakteryzujących się strefami KN. W połączeniu, np. z badaniami ultradźwiękowymi, określa się rozmiary i położenie konkretnej wady.
Ocena stanu technicznego rurociągów - lokalizacja nieciągłości metalu / wad
Rys. 7a przedstawia rozkład magnetycznego pola rozproszonego zmierzonego wzdłuż tworzącej rurociągu. Występuje tu charakterystyczna zmiana znaku pola Hp na niewielkiej długości, która świadczy o powstaniu nieciągłości / wady.
Rys. 7b ilustruje rozkład magnetycznego pola rozproszonego zmierzony po obwodzie rury w miejscu zlokalizowanej wady. Stwierdzono, że jeśli odległość między liniami koncentracji naprężeń KN wynosi jedną do dwóch grubości ścianki, to takie wyniki pomiarów wskazują na niebezpieczną nieciągłość. Taką sytuację dokumentuje zdjęcie w lewym górnym rogu Rysunku 7, wykonane po wymianie uszkodzonego fragmentu rurociągu.
Już od końca lat 90-tych posiadamy matematyczno-fizyczny model charakteryzujący związek naprężeń i odkształceń w rurociągach z rozkładem magnetycznego pola rozproszonego.
Badanie metodą MPM płaszczy i dennic zbiorników ciśnieniowych
Rys. 8 przedstawia rozkład linii KN wykrytych podczas badań na dużym zbiorniku ciśnieniowym. Przebieg linii KN wskazuje na zwiększone obciążenie jednej z podpór oddziałujące na płaszcz zbiornika. Może to sugerować niewłaściwe posadowienie zbiornika.
Badania nieniszczące metodą MPM są efektywne przy ocenie pozostałego czasu pracy (resursu) obiektów przemysłowych.
Badania metodą MPM można stosować do wyboru reprezentacyjnych próbek metalu w celu dalszych badań w laboratorium. Obecnie jest to jedyna metoda diagnostyki, która pozwala szybko określić strefy wad metalu w nowych wyrobach i z wysoką dokładnością określić powstające uszkodzenia w urządzeniach pracujących. Jako jedyna spośród metod badań nieniszczących zdaje egzamin przy wykrywaniu niespodziewanych uszkodzeń zmęczeniowych w urządzeniach.
Na 50-tym kongresie Międzynarodowego Instytutu Spawalnictwa (MIS), który odbył się w San Francisco (lipiec 1997), badania metodą MPM zostały zarekomendowane przez MIS do stosowania ich do oceny stanu połączeń spawanych w urządzeniach.
W Rosji, gdzie metodę opracowano, stosuje się w praktyce procedury badań metodą MPM dla wielu gałęzi przemysłu. Są to zasady kontroli rurociągów, zbiorników ciśnieniowych, łopatek, wirników i tarcz turbin parowych i gazowych oraz połączeń spawanych w różnych konstrukcjach.
Kolejne dwie grafiki ilustrują badania metodą MPM powierzchni wewnętrznej reaktora polimeryzacji polichlorku winylu. Przykład przedstawia stan zlokalizowanej, wadliwej spoiny dennicy reaktora.
Rozkład magnetycznego pola Hp wzdłuż spoiny dennicy przed naprawą pęknięcia
i strefy maksymalnej koncentracji naprężeń (KN)
Wyniki kontroli przed naprawą spoiny dennicy reaktora R-701/1 Anwil S.A Włocławek
Zachęcamy do zapoznania się z danymi i przykładami zastosowania badań metodą MPM podanymi na wszystkich stronach wskazanych niżej. Metoda Magnetycznej Pamięci Metalu to w skrócie mMPM, zaś stosując pełny opis jest to:
metoda badań nieniszczących wykorzystująca zjawisko Magnetycznej Pamięci Metalu występujące w ferromagnetykach. Ferromagnetyki (stale ferromagnetyczne) zawierają metale takie jak żelazo, nikiel lub kobalt oraz inne pierwiastki w odpowiedznich proporcjach.
badania NDT | początki mMPM | mMPM na świecie | mMPM w trakcie remontu | mMPM w trakcie eksploatacji | mMPM + inne badania NDT | przykłady badań NDT